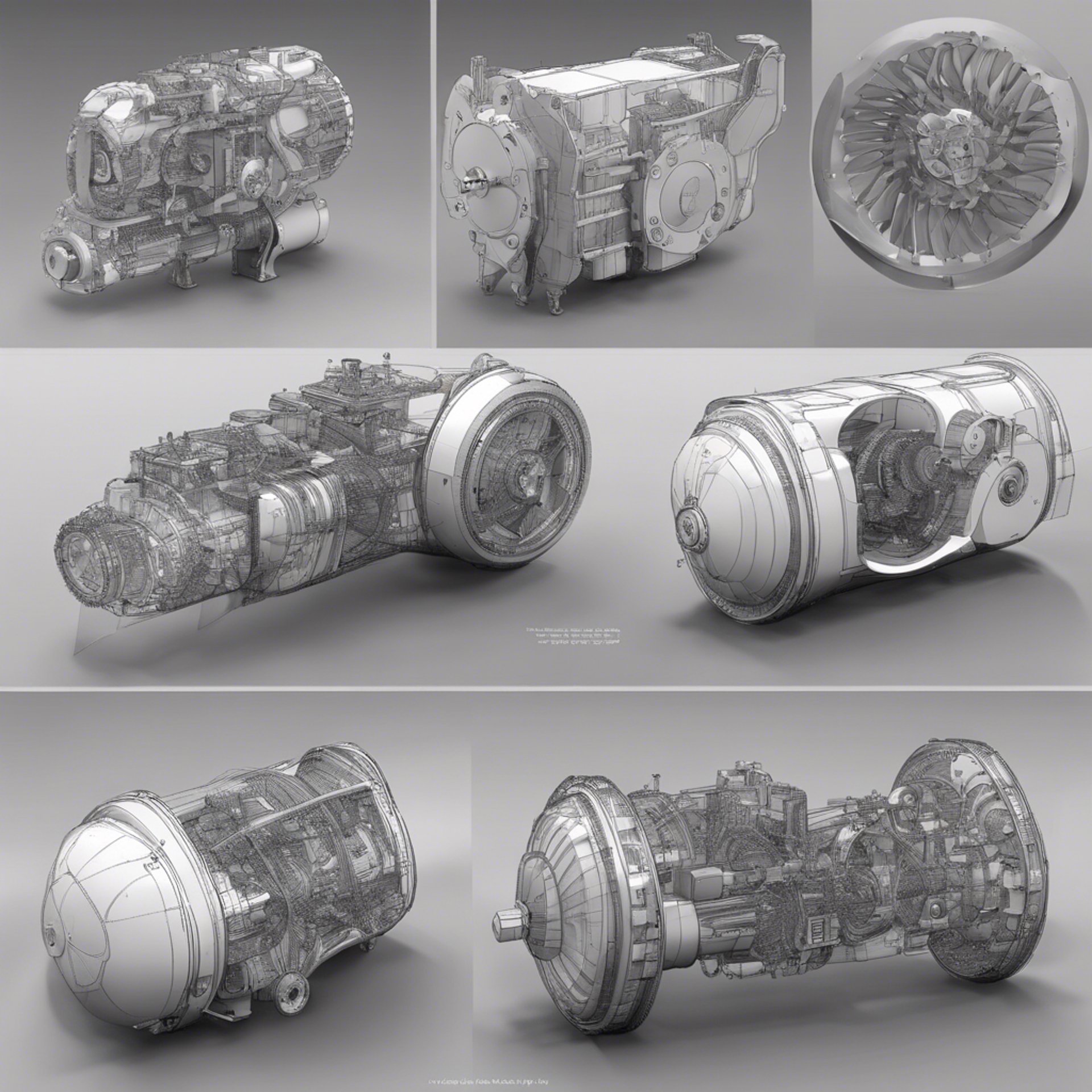
MOTOR TECHNOLOGIES
WE DELIVER
BLDC
Brushless DC (BLDC) motors are electric motors that operate using direct current (DC) electricity and do not have brushes. Unlike traditional brushed motors, BLDC motors use electronic commutation to control the current flow within the motor, which results in several performance and efficiency benefits.
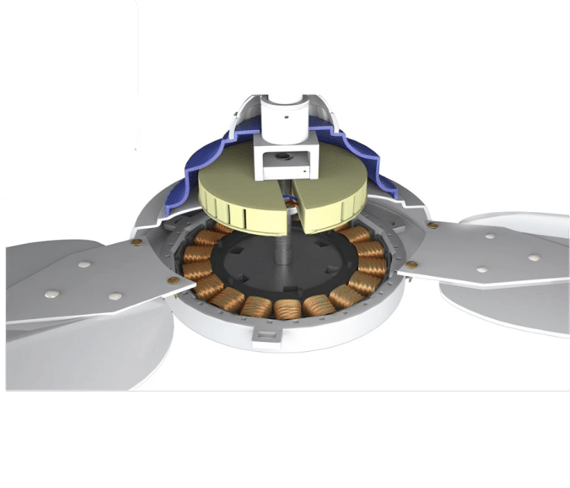
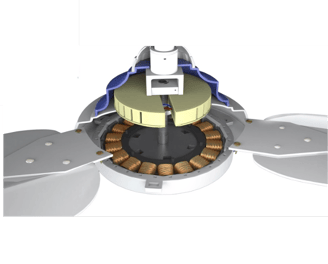
Advantages
High efficiency
Long lifespan
Low maintenance
High power density
Better speed control
Disadvantages
Higher initial cost
Complex control systems
EMI issues
Torque ripple
PMSM
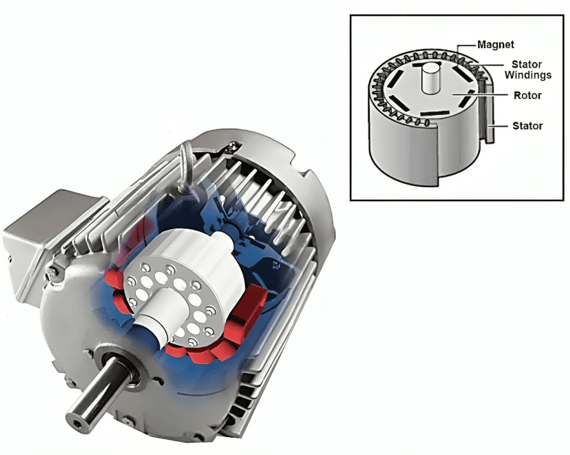
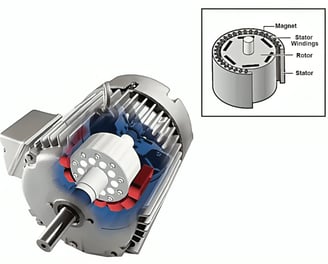
Permanent Magnet Synchronous Motors (PMSMs) are electric motors that utilize permanent magnets embedded in the rotor to generate a consistent magnetic field. Known for their high efficiency and superior performance, PMSMs are widely used in various applications, including industrial machinery, robotics, and electric vehicles.
Advantages
Disadvantages
High efficiency
High power density
Precise speed and position control
Low maintenance
High reliability
Complex control requirements
Sensitivity to temperature
Risk of demagnetization
Dependence on rare earth materials for magnets
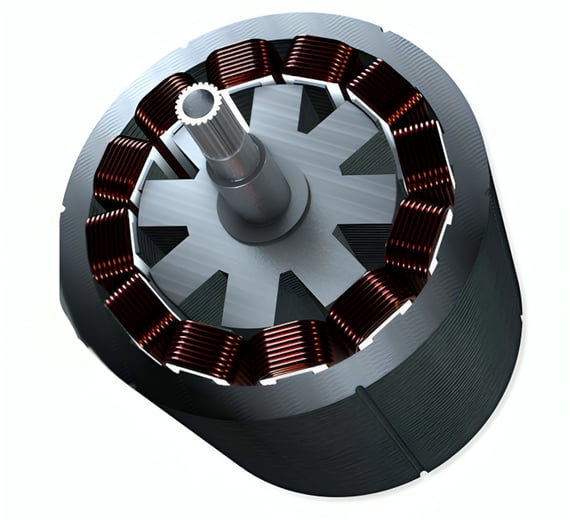
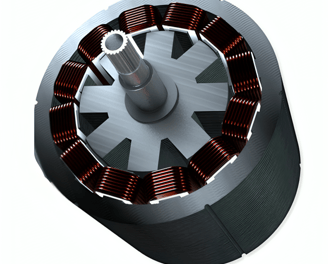
SRM
Switched Reluctance Motors (SRMs) are electric motors that operate based on the principle of reluctance torque. The rotor in an SRM is made of a soft magnetic material with salient poles, and it does not contain any windings or permanent magnets. The stator contains coils that are sequentially energized to create a magnetic field, causing the rotor to move to minimize the reluctance path.
Advantages
Simple and robust construction
High reliability
High efficiency, especially at low speeds
Low cost due to the absence of permanent magnets
Wide operational speed range
Disadvantages
Torque ripple leading to vibrations and noise
Complex control systems required
Acoustic noise during operation
Magnetic saturation limiting high torque performance
Limited suitability for applications requiring smooth and quiet operation
PMDC Brush Motor
A Permanent Magnet DC (PMDC) brushed motor uses permanent magnets to create a magnetic field and brushes to transfer electricity to the rotating armature. The permanent magnets in the stator provide a constant magnetic field, while the armature carries windings that generate a magnetic field when DC voltage is applied. The commutator, attached to the armature, reverses the current direction as the motor turns, with brushes transferring electric current to the commutator. This interaction produces torque, causing the rotor to turn.
Advantages
Disadvantages
Simple construction
Cost-effective
Good starting torque
Easy speed control
Reliable performance
Brush wear
Electrical noise
Lower efficiency
Limited lifespan
Heat generation
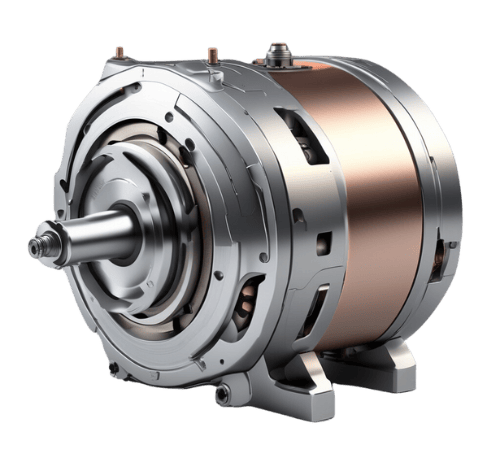
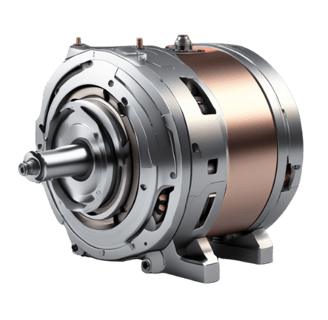
SynRM
A Synchronous Reluctance Motor (SynRM) operates on the principle of magnetic reluctance, where the rotor aligns with the stator's rotating magnetic field to minimize resistance. The stator has a laminated iron core with windings connected to an AC power supply, while the rotor consists of laminated iron segments separated by non-magnetic materials, with no windings or magnets. This simple construction makes the motor robust, efficient, and low-maintenance.
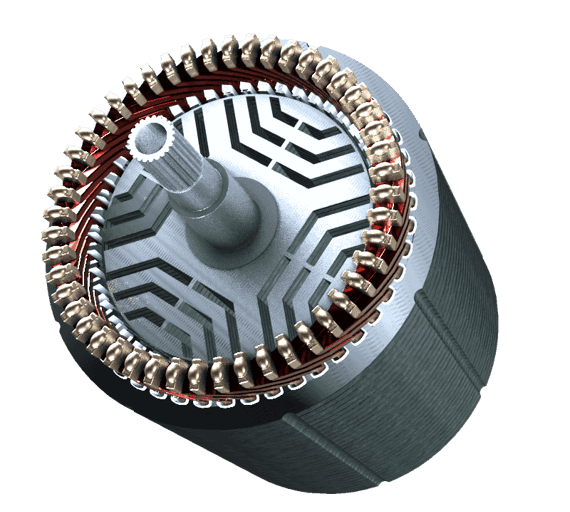
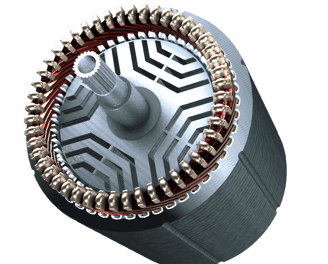
Advantages
Disadvantages
High efficiency
Simple and robust rotor construction
Low maintenance
Cost-effective compared to PMSMs
No rotor copper losses
Lower power density compared to PMSMs
Requires precise control systems
Higher initial cost than induction motors
Limited torque at low speeds
Less established technology, fewer available models
Technologies
© 2024. All rights reserved.
Connect With Us
Stay connected and follow us on our social media platform for the latest news and updates.